
You’ll hear some very convincing arguments about how the selective (conical) plastic thrust spacer is used to adjust the stack height on the GM
298mm torque converter. You will also hear some very convincing arguments about how this same selective thrust spacer is used to adjust the clutch release clearance on the GM 298mm torque converter. The truth is that both statements are correct. The selective (conical) plastic thrust spacer may be used to adjust both the stack height and clutch release clearance on the 298 converter.
What is important is that you are aware that making a change to one adjustment also changes the other. As long as you are aware of the proper parameters and the parameter limits of both measurements, you can make successful adjustments to both.
The selective (conical) plastic thrust spacer fills the void between the cover and the turbine hub. Spacers are made in six different thicknesses, numbered 2 through 7 (see Figure 1). They vary in thickness between 14.6mm (.575") and 16.8mm (.661").
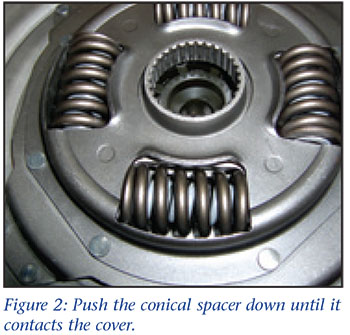
The different thicknesses of the spacers are used to vary the distance between the cover and the turbine hub. The O.D. of the spacer has an o-ring that makes a hydraulic seal between the spacer and the TCC clutch plate. The I.D. of the spacer has a clearance fit on the smooth front surface of the turbine shaft (input). It is in contact with the o-ring on the turbine shaft and also makes a hydraulic seal.
The front thrust surface of the spacer is in contact with the cover, and the rear thrust surface is in contact with the turbine hub. The turbine shaft, turbine hub, TCC clutch and conical spacer all rotate at the same speed. The conical spacer is not splined or affixed to the other members of the unit, but the drag of the 2 o-rings and the hydraulic force on the spacer keep it rotating with the other members. The damper assembly of the TCC clutch is splined to the turbine hub, so they rotate at the same speed. The distance between the cover and the turbine hub is governed by which selective thrust spacer has been chosen. Once the thrust spacer is in place, the distance between the two parts remains the same, but the TCC clutch is free to travel between the cover and the turbine hub. The TCC clutch is hydraulically forced forward for TCC apply and hydraulically forced rearward for TCC release.
To check the clutch release clearance, place a selective thrust spacer, preferably with a fresh o-ring, into the TCC clutch plate. Put the clutch plate into the cover. The friction material of the clutch plate should be resting on the mating surface of the cover. Push the selective spacer (see Figure 2) down until it contacts the cover. This is the relative position of the spacer to the clutch plate while in TCC apply.
Gently remove the plate from the cover and measure the height of the spacer that protrudes above the cover (see Figure 3). This particular measurement was about .090". Now take the clutch plate and place it onto the turbine hub. Push it down until the splines of the damper assembly bottom on the turbine hub. This will force the selective spacer up, exposing more of the spacer.
Again, measure the height of the spacer that protrudes above the cover. On this particular one (see Figure 4), it now measures .140". Since this is now the relative position of the spacer to the clutch plate in the TCC release position, subtracting measurement 1 from measurement 2 will be the clutch release clearance. In this case it is .050". Since .030" to .060" is desirable clutch release clearance, this converter will be fine as long as the average overall height falls within the 5.855 minimum and the 5.905 maximum measurements. If you needed less clearance you could replace the spacer with a thinner one, and if you needed more clearance you could replace the spacer with a thicker one. Fortunately, when the mating parts of a converter are machined for trueness, both the stack height and the release clearance usually become less. For this reason, increasing the selective spacer by a number or two will usually bring both measurements back to proper specs.
Responsibility and Liability
It is a common practice in the
transmission field to increase line pressure to enhance transmission performance. Increasing line pressure also has a direct effect on the converter pressures. Granted, an increase in TCC apply pressure may help the clutch hold as the demands on the clutch increase, but these benefits come with a price. As line pressure increases, converter head pressure and heat also increase. Along with this, converter charge oil and cooler flow decrease. Since converter charge oil becomes the transmission’s lube oil when it leaves the converter, this is not a good thing for the converter or the transmission. It is a common practice in the transmission field to increase line pressure to enhance transmission performance. Increasing line pressure also has a direct effect on the converter pressures. Granted, an increase in TCC apply pressure may help the clutch hold as the demands on the clutch increase, but these benefits come with a price. As line pressure increases, converter head pressure and heat also increase. Along with this, converter charge oil and cooler flow decrease. Since converter charge oil becomes the transmission’s lube oil when it leaves the converter, this is not a good thing for the converter or the transmission.
The transmission rebuilder seldom sees the inside of the torque converter. He may not be aware of the damage he is causing by making his modifications. But on the other hand, when the converter rebuilder sees excessive wear between the selective spacer and the cover, (obviously too much converter pressure), he is not helping himself or the transmission rebuilder by not saying anything. This is where better communication is needed.